Maximizing Your Welding WPS: Strategies for Improved Efficiency and Effectiveness
Maximizing Your Welding WPS: Strategies for Improved Efficiency and Effectiveness
Blog Article
Grasping Welding WPS Specifications: Best Practices and Techniques for Quality Welds
In the realm of welding, mastering Welding Treatment Requirements (WPS) standards is a crucial part that directly influences the high quality and integrity of welds. As we navigate with the intricacies of welding WPS criteria, uncovering vital insights and methods for attaining top-tier welds will certainly be vital for welders seeking to succeed in their craft and create welds that stand the examination of time.
Recognizing Welding WPS Requirements
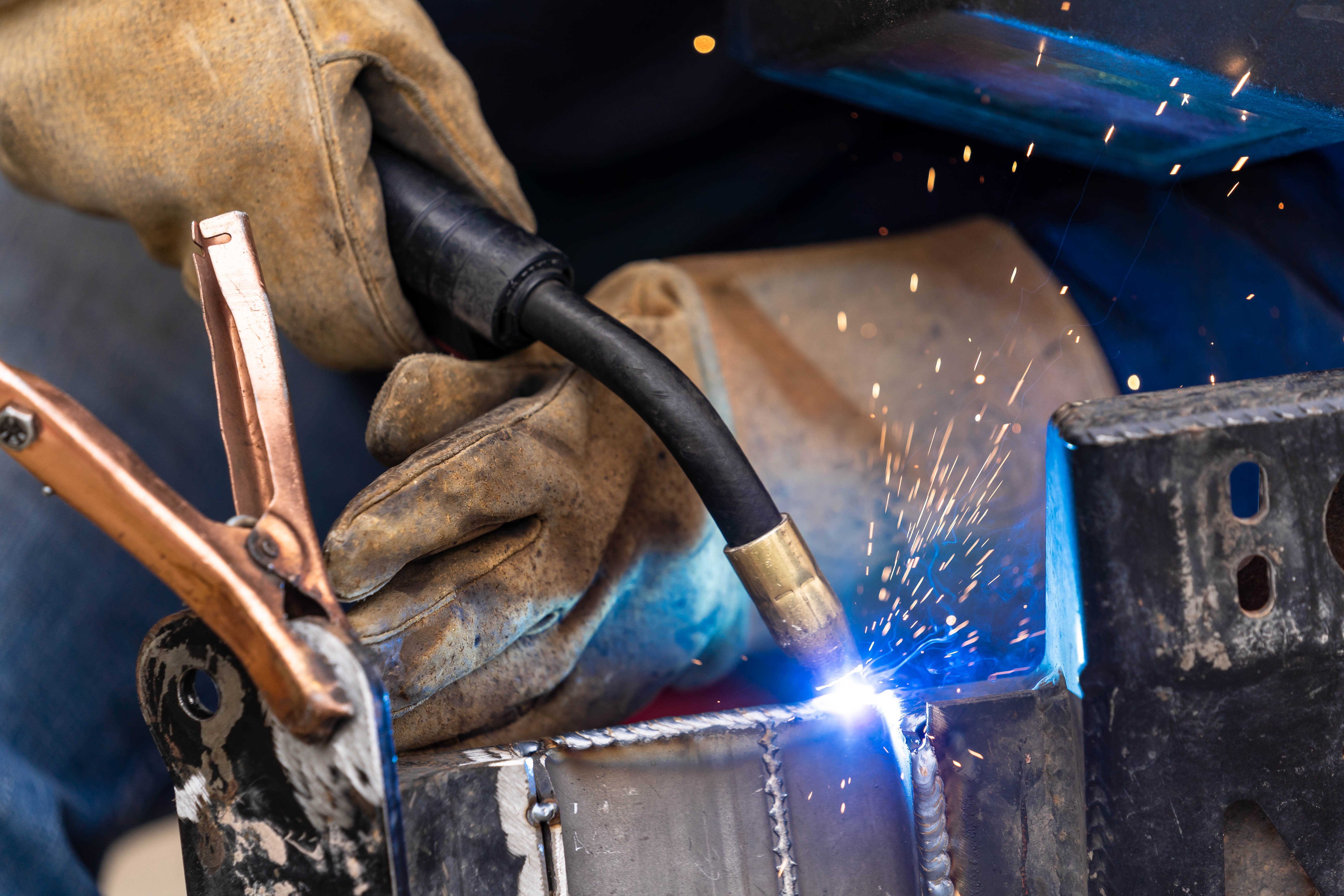
Understanding WPS criteria is essential for inspectors, designers, and welders associated with welding procedures. By adhering to WPS guidelines, welders can create welds that satisfy the needed mechanical residential properties and architectural stability. Assessors depend on WPS documentation to validate that welding treatments are being complied with properly and that the resulting welds are of excellent quality. Engineers use WPS criteria to make welding procedures that ensure the toughness and dependability of welded structures.
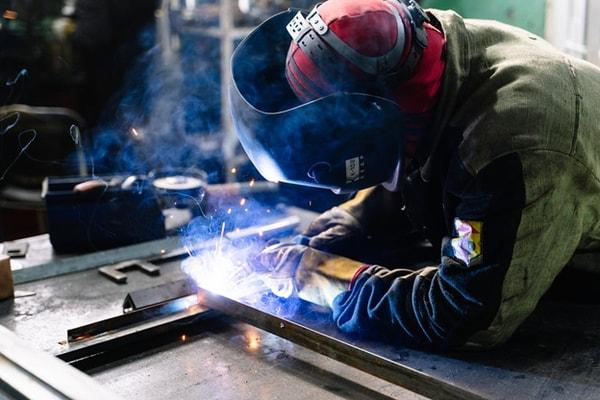

Essential Devices for Quality Welds
Grasping welding WPS standards is vital for welders to properly utilize the crucial tools needed for creating quality welds. The type of welding machine required depends on the welding procedure being used, such as MIG, TIG, or stick welding. Wire brushes and damaging hammers are essential for cleaning the weld joint prior to and after welding to remove any type of contaminations that can affect the high quality of the weld.
Trick Strategies for Welding Success
To accomplish welding success, one need to master the crucial techniques necessary for generating top quality welds. One essential method is maintaining the right arc size. Maintaining the electrode at the optimum distance from the workpiece is important for developing solid, uniform welds. In addition, regulating the traveling speed is extremely important. Relocating too promptly can result in inadequate infiltration, while relocating too gradually can cause too much warm input and possible flaws. Correct control of the electrode angle is an additional crucial technique. The angle at which the electrode is held can influence the bead shape and penetration of the weld. Moreover, making certain regular weapon angle and direction of travel is vital for uniformity in the weld grain. Finally, preserving a stable welding and a steady hand position throughout the procedure is vital to accomplishing precision and uniformity in the welds. By mastering see this website these essential strategies, welders can raise the high quality of their work and attain welding success.
Ensuring Conformity With WPS Specifications
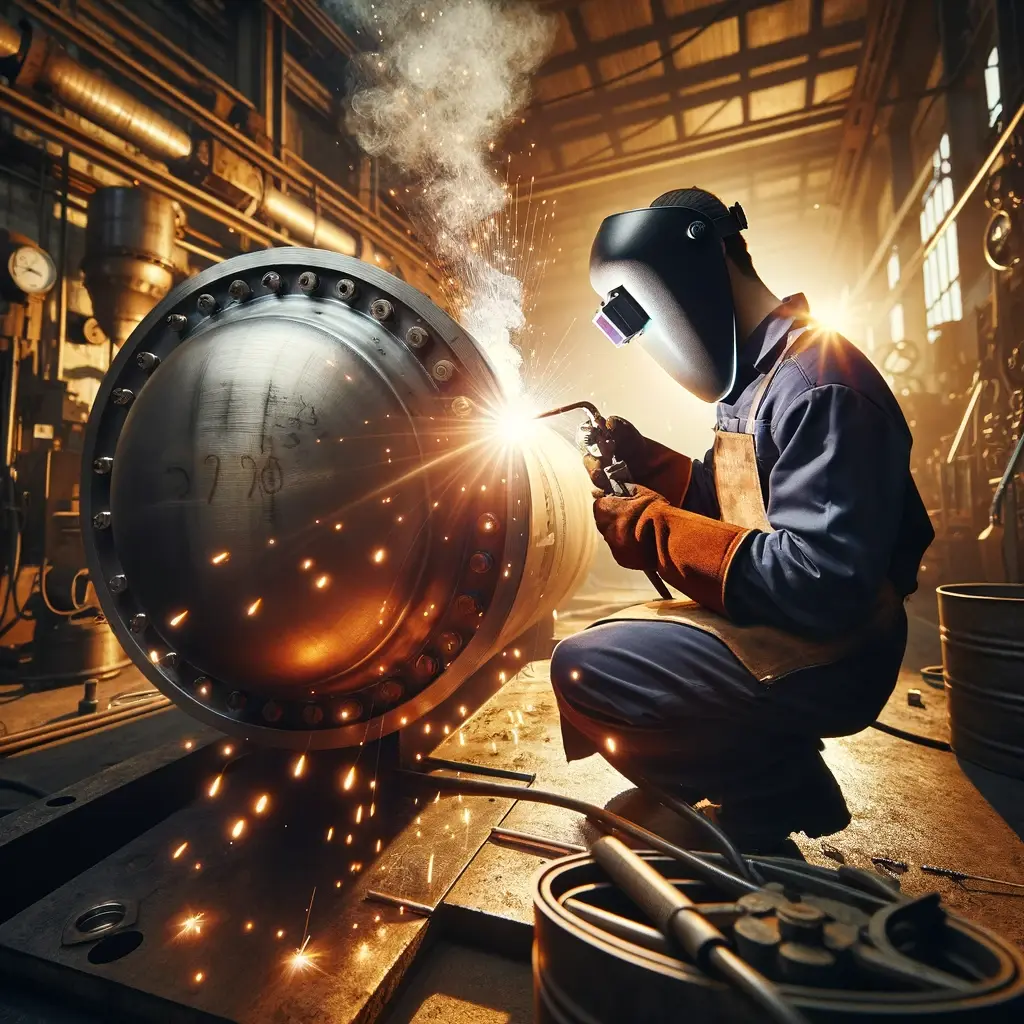
Additionally, keeping thorough documents of welding parameters, devices calibration, and examination results is critical for demonstrating conformity with WPS criteria. By faithfully adhering to WPS criteria, welders can make certain that their job satisfies the necessary high quality degrees and contributes to the general success of the welding job.
Troubleshooting Common Welding Issues
When confronted with common welding concerns, identifying the source is crucial for reliable troubleshooting. One common problem is the visibility of porosity in welds, frequently caused by contaminants such as oil, rust, or wetness. To address this, making certain appropriate cleansing of the base steel prior to welding and using the appropriate protecting gas can dramatically reduce porosity. Another issue regularly encountered is absence of fusion, where the weld stops working to correctly bond with the base product. This can stem from poor warmth input or inappropriate welding strategy. Readjusting parameters such as voltage, wire feed speed, or travel speed can assist improve blend. Furthermore, distortion, splitting, and spatter prevail welding difficulties that can be minimized through proper joint preparation, consistent heat control, and choosing the ideal welding consumables. By thoroughly understanding these usual welding issues and their source, welders can successfully fix issues and achieve high-quality welds.
Conclusion
Finally, understanding welding WPS criteria requires a detailed understanding of the guidelines, making use of necessary tools, and carrying out key strategies for successful welds. Making sure conformity with WPS standards is vital for creating high quality welds and preventing typical welding concerns. By following best techniques and strategies, welders can achieve consistent and dependable cause their welding tasks.
In the realm of welding, grasping Welding Procedure Requirements (WPS) requirements is an essential component that directly affects the high quality and stability of welds.When delving right into the realm of welding methods, a critical element to comprehend is the value and details of Welding Procedure Spec (WPS) criteria. WPS requirements give a comprehensive guideline for welding procedures, guaranteeing consistency, top quality, and safety and security in the welding process. The type of welding maker needed depends on the welding procedure being used, such as MIG, TIG, or stick welding.Accomplishing welding success with the proficiency of Click Here vital methods requires a thorough understanding and adherence to Welding Treatment Requirements (WPS) standards.
Report this page